
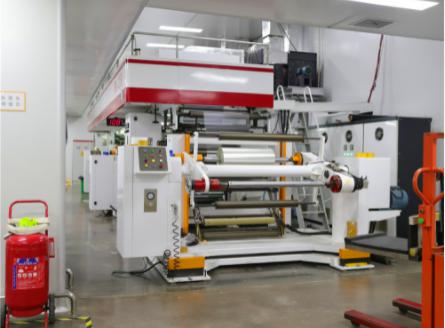
In the long-term printing process, the ink gradually loses its fluidity, and the viscosity increases abnormally, which makes the ink jelly-like, The subsequent use of the residual ink is more difficult.
Abnormal reason:
1,When the solvent in the printing ink is volatilized, the dew generated by the external low temperature is mixed into the printing ink (especially easy to occur in the unit where the consumption of printing ink is very small).
2,When the ink with high affinity with water is used, the new ink will thicken abnormally.
Solutions:
1,Quick-drying solvents should be used as much as possible, but sometimes a small amount of water will enter the printing ink when the temperature is high and humid. If an abnormality occurs, new ink should be replenished or replaced in time. The residual ink used repeatedly should be filtered or discarded regularly due to the involvement of water and dust.
2,Discuss abnormal thickening with the ink manufacturer, and improve the ink formulation if necessary.
Odor (solvent residue):The organic solvent in the printing ink will be mostly dried in the dryer instantly, but the residual trace solvent will be solidified and transferred to the original film to remain. The amount of high-concentration organic solvent residues in the printed matter directly determines the odor of the final product. Whether it is abnormal can be judged by smelling the nose. Of course, with the advancement of science and technology, smelling through the nose has fallen behind significantly. For items with higher requirements for solvent residues, professional instruments can be used to measure them.
Abnormal reason:
1,Printing speed is too fast
2, Inherent properties of resins, additives and binders in printing inks
3,The drying efficiency is too low or the drying method is lacking
4,The air duct is blocked
Solutions:
1. Appropriately reduce the printing speed
2. The situation of residual solvent in printing ink can be negotiated with the ink manufacturer to take precautions. The use of quick-drying solvent only makes the solvent evaporate quickly, and does not have much effect on reducing the residual amount of solvent
3. Use fast-drying solvent or low-temperature drying (fast-drying will make the surface of the ink crusted, which will affect the evaporation of the internal solvent. Slow-drying is effective in reducing the residual amount of solvent.)
4. Since the residual organic solvent is also related to the type of the original film, the amount of the residual solvent varies with the type of the original film. When appropriate, we can discuss the problem of solvent residue with the original film and ink manufacturers.
5. Regularly clean the air duct to make it exhaust smoothly
Post time: Apr-14-2022