Facial mask bags are soft packaging materials.
From the perspective of main material structure, aluminized film and pure aluminum film are basically used in the packaging structure.
Compared with aluminum plating, pure aluminum has a good metallic texture, is silvery white, and has anti-gloss properties; aluminum has soft metal properties, and products with different composite materials and thicknesses can be customized according to requirements, which meets the pursuit of thick texture in high-end products and makes high-end facial masks It is more intuitively reflected from the packaging.
Because of this, facial mask packaging bags have evolved from basic functional requirements at the beginning to high-end requirements with simultaneous increases in performance and texture, which has promoted the transformation of facial mask bags from aluminum-plated bags to pure aluminum bags.
Material: aluminium, pure aluminum, all-plastic composite bag, paper-plastic composite bag. Pure aluminum and aluminum-plated materials are commonly used, and all-plastic composite bags and paper-plastic composite bags are less commonly used.
Number of layers: commonly used three and four layers
Typical structure:
Pure aluminum bag three layers: PET/pure aluminum foil/PE
Four layers of pure aluminum bags: PET/pure aluminum foil/PET/PE
Aluminium bag three layers: PET/VMPET/PE
Four layers of aluminium bags: PET/VMPET/PET/PE
Full plastic composite bag: PET/PA/PE
Barrier properties: aluminum>VMPET>all plastic
Ease of tearing: four layers > three layers
Price: pure aluminum>aluminized>all plastic,
Surface effect: glossy (PET), matte (BOPP),UV, emboss
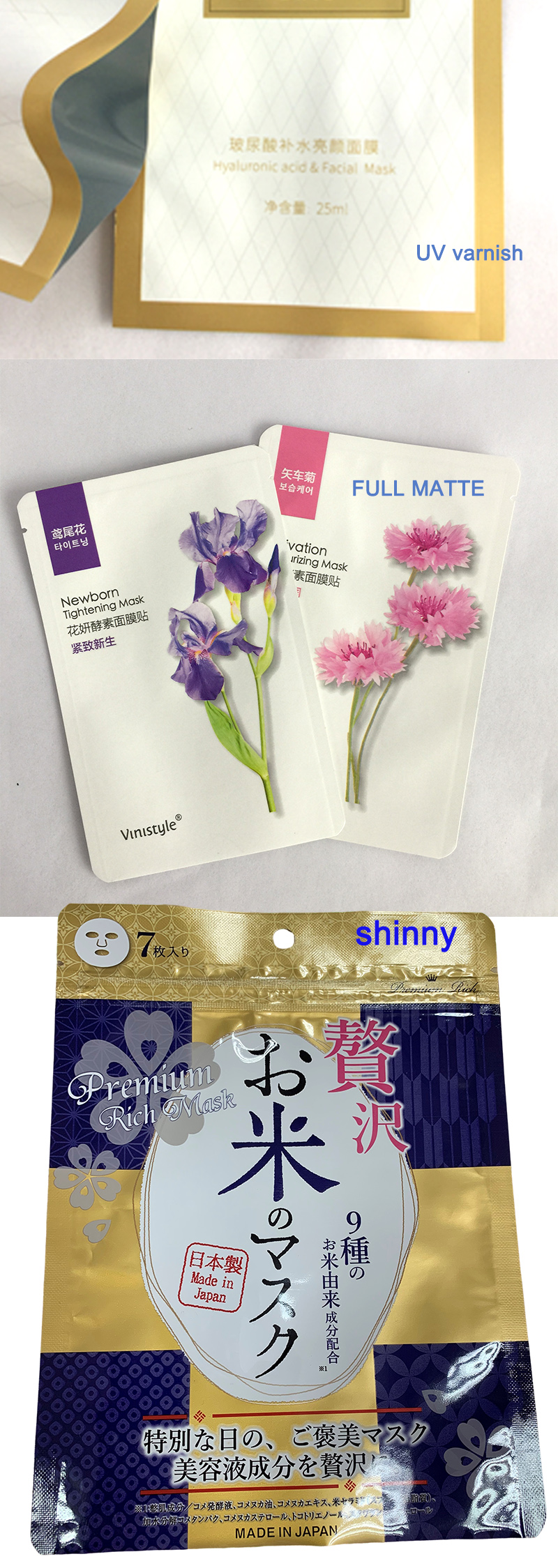
Bag shape: special-shaped bag, spout bag, flat pouches,doypack with zip
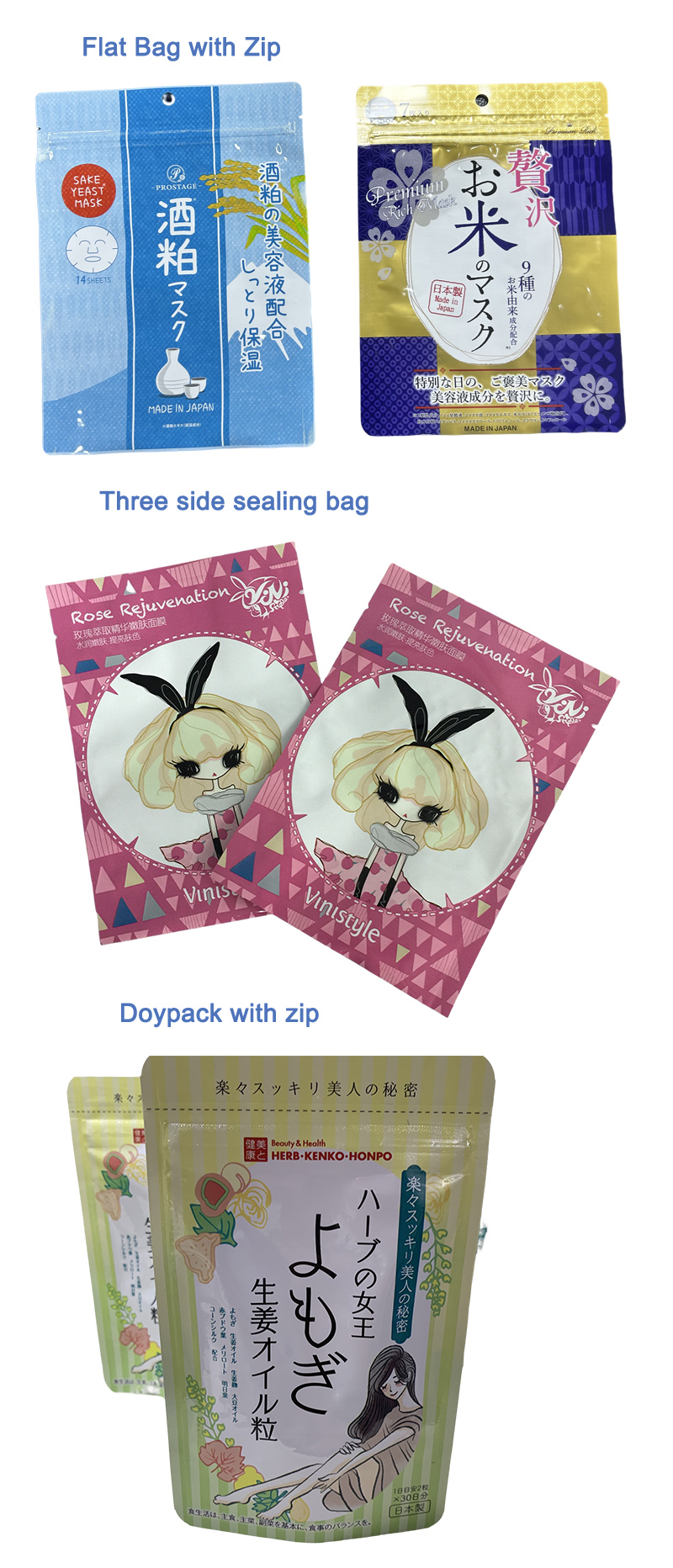
Key Points For Production Control Of Facial Mask Packaging Bags
Film bag thickness: conventional 100microns-160microns, the thickness of pure aluminum foil for composite use is usually 7microns
Production lead time: expected to be about 12 days
Aluminium film: VMPET is a composite flexible packaging material formed by plating an extremely thin layer of metallic aluminum on the surface of a plastic film using a special process. The advantage is a metallic luster effect, but the disadvantage is poor barrier properties.
1.Printing Procedure
From the current market requirements and consumer point of view, facial masks are basically regarded as high-end products, so the most basic decoration requirements are different from those of ordinary food and daily chemical packaging, at least they are "high-end" consumer psychology. So for printing, taking PET printing as an example, the overprint accuracy and hue requirements of its printing are at least one level higher than other packaging requirements. If the national standard is that the main overprint accuracy is 0.2mm, then the secondary positions of facial mask packaging bag printing basically need to meet this printing standard in order to better adapt to customer requirements and consumer needs.
In terms of color difference, customers for facial mask packaging are also much stricter and more detailed than ordinary food companies.
Therefore, in the printing process, companies that produce facial mask packaging must pay attention to control over printing and hue. Of course, there will also be higher requirements for printing substrates to adapt to the high standards of printing.
2.Lamination procedure
Composite mainly controls three major aspects: composite wrinkles, composite solvent residue, composite pitting and bubbles and other abnormalities. In this process, these three aspects are the key factors affecting the yield of facial mask packaging bags.
(1) Compound wrinkles
As can be seen from the above structure, facial mask packaging bags mainly involve the compounding of pure aluminum. Pure aluminum is rolled from pure metal into a very thin film-like sheet, commonly known as "aluminum film" in the industry. The thickness is basically between 6.5 and 7 μm. Of course, there are also thicker aluminum films.
Pure aluminum films are very prone to wrinkles, breaks, or tunnels during the lamination process. Especially for laminating machines that automatically splice materials, due to the irregularities in the automatic bonding of the paper core, it is easy to be uneven, and it is very easy for the aluminum film to wrinkle directly after lamination, or even die.
For wrinkles, on the one hand, we can remedy them in the post-process to reduce the losses caused by wrinkles. When the composite glue is stabilized to a certain state, re-rolling is one way, but this is only a way to reduce it; on the other hand, we can start from the root cause. Reduce the amount of winding. If you use a larger paper core, the winding effect will be more ideal.
(2) Composite solvent residue
Since facial mask packaging basically contains aluminized or pure aluminum, for composites, the presence of aluminized or pure aluminum is detrimental to the volatilization of solvents. This is because the barrier properties of these two are stronger than other general materials, so It is detrimental to the volatilization of solvents. Although it is clearly stated in the GB/T10004-2008 "Dry Composite Extrusion Compounding of Plastic Composite Films and Bags for Packaging" standard: This standard does not apply to plastic films and bags made of plastic materials and paper base or aluminum foil.
However, currently facial mask packaging companies and most companies also use this national standard as the standard. For aluminum foil bags, this standard is also required, so it is somewhat misleading.
Of course, the national standard does not have clear requirements, but we still have to control solvent residues in actual production. After all, this is a very critical control point.
As far as personal experience is concerned, it is feasible to make effective improvements in terms of glue selection, production machine speed, oven temperature, and equipment exhaust volume. Of course, this aspect requires analysis and improvement of specific equipment and specific environments.
(3) Compound pitting and bubbles
This problem is also mainly related to pure aluminum, especially when it is a composite PET/AL structure, it is more likely to appear. The composite surface will accumulate a lot of "crystal point"-like phenomena, or similar "bubble" point-like phenomena. The main reasons are as follows:
In terms of base material: The surface treatment of the base material is not good, which is prone to pitting and bubbles; the base material PE has too many crystal points and is too large, which is also a major cause of problems. On the other hand, the particle aspect of the ink is also one of the factors. The leveling properties of the glue and the coarser particles of the ink will also cause similar problems during bonding.
Furthermore, in terms of machine operation, when the solvent is not evaporated enough and the compounding pressure is not high enough, similar phenomena will also occur, either the gluing screen roller is clogged, or there is foreign matter.
Look for better solutions from the above aspects and judge or eliminate them in a targeted manner.
3. Bag making
At the control point of the finished product process, we mainly look at the flatness of the bag and the strength and appearance of the edge sealing.
In the finished bag making process, smoothness and appearance are relatively difficult to grasp. Because its final technical level is determined by machine operation, equipment, and employee operating habits, the bags are very easy to be scratched during the finished product process, and abnormalities such as large and small edges may appear.
For facial mask bags with strict requirements, these are definitely not allowed. To solve this problem, we might as well manage the machine from the most basic 5S aspect to control the scratching phenomenon.
As the most basic workshop environment management, the cleaning of the machine is one of the basic production guarantees to ensure that the machine is clean and that no foreign objects appear on the machine to ensure normal and smooth work. Of course, we need to change the most basic and specific operating requirements and habits of the machine.
In terms of appearance, in terms of edge sealing requirements and edge sealing strength, it is generally required to use a sealing knife with finer texture or even a flat sealing knife to press the edge sealing. This is a rather special request. It is also a big test for the machine operators.
4. Selection of base materials and auxiliary materials
Point is its key production control point, otherwise many abnormalities will occur during our compounding process.
The liquid of the facial mask will basically contain a certain proportion of alcohol or alcoholic substances, so the glue we choose needs to be medium-resistant glue.
Generally speaking, during the production process of facial mask packaging bags, many details need to be paid attention to, because the requirements are different and the loss rate of soft packaging companies will be relatively high. Therefore, every detail of our process operations must be very meticulous to improve the yield rate, so that we can stand on the commanding heights in the market competition of this type of packaging.
Related keywords
Custom Face Mask Packaging,facial mask packaging bags supplier
Post time: Feb-02-2024