This glossary covers essential terms related to flexible packaging pouches and materials, highlighting the various components, properties, and processes involved in their production and use. Understanding these terms can aid in the selection and design of effective packaging solutions.
Here's a glossary of common terms related to flexible packaging pouches and materials:
1.Adhesive: A substance used for bonding materials together, often used in multi-layer films and pouches.
2.Adhesive Lamination
A laminating process in which individual layers of packaging materials are laminated to each other with an adhesive.
3.AL - Aluminium Foil
A thin gauge (6-12 microns) aluminium foil laminated to plastic films to provide maximum oxygen, aroma and water vapour barrier properties. Although it is by far the best barrier material, it is increasingly being replaced by metallised films, (see MET-PET, MET-OPP and VMPET) because of cost.
4.Barrier
Barrier Properties: The ability of a material to resist the permeation of gases, moisture, and light, which is critical in extending the shelf life of packaged products.
5.Biodegradable: Materials that can break down naturally into non-toxic components in the environment.
6.CPP
Cast Polypropylene film. Unlike OPP, it is heat sealable, but at much higher temperatures than LDPE, thus it is used as a heat-seal layer in retort able packaging. It is, however, not as stiff as OPP film.
7.COF
Coefficient of friction, a measurement of “slipperiness” of plastic films and laminates. Measurements are usually done film surface to film surface. Measurements can be done to other surfaces as well, but not recommended, because COF values can be distorted by variations in surface finishes and contamination on test surface.
8.Coffee Valve
A pressure relief valve added to coffee pouches to allow natural unwanted gasses to be vented whilst maintaining the freshness of the coffee. Also called an aroma valve as it allows you to smell the product through the valve.
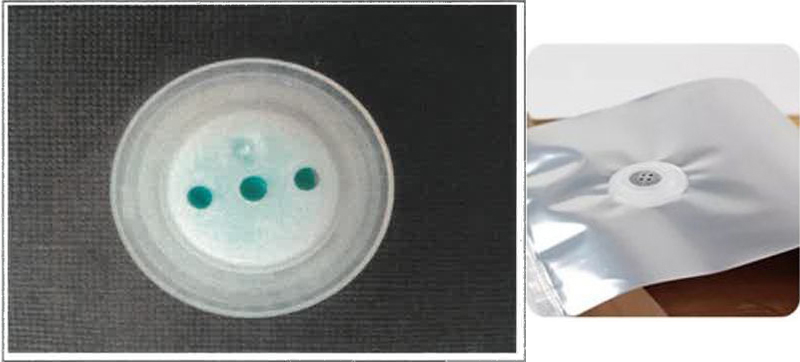
9.Die-Cut Pouch
A pouch that is formed with contour side seals that then passes through a die-punch to trim excess sealed material, leaving a contoured and shaped final pouch design. Can be accomplished with both stand up and pillow pouch types.
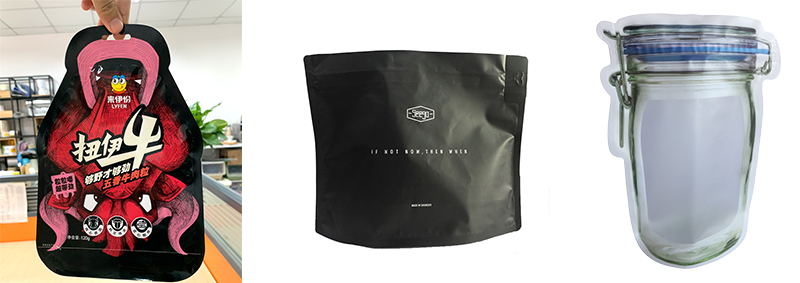
10.Doy Pack (Doyen)
A stand-up pouch that has seals on both sides and around the bottom gusset. In 1962, Louis Doyen invented and patented the first soft sack with an inflated bottom called Doy pack. Although this new packaging was not the immediate success hoped for, it is booming today since the patent has entered the public domain. Also spelt - Doypak, Doypac, Doy pak, Doy pac.
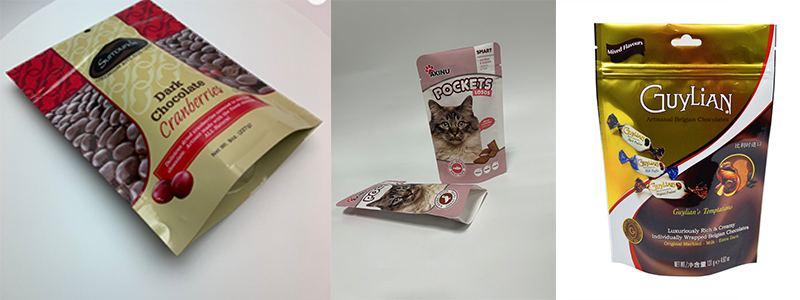
11.Ethylene Vinyl Alcohol (EVOH): A high-barrier plastic often used in multilayer films to provide excellent gas barrier protection
12.Flexible Packaging: Packaging made from materials that can be easily bent, twisted, or folded, typically including pouches, bags, and films.
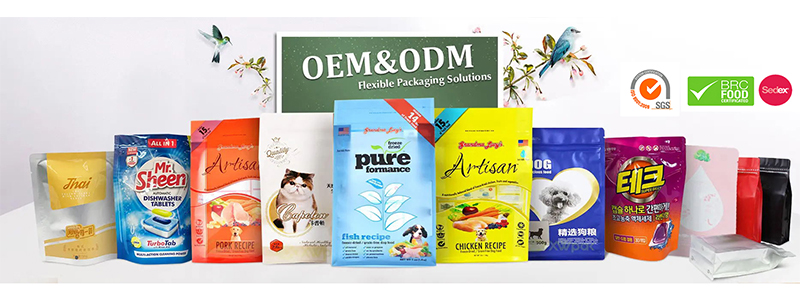
13.Gravure Printing
(Rotogravure). With gravure printing an image is etched on the surface of a metal plate, the etched area is filled with ink, then the plate is rotated on a cylinder that transfers the image to the film or other material. Gravure is abbreviated from Rotogravure.
14.Gusset
The fold in the side or bottom of the pouch, allowing it to expand when contents are inserted
15.HDPE
High density, (0.95-0.965) polyethylene. This part has much higher stiffness, higher temperature resistance and much better water vapour barrier properties than LDPE, although it is considerably hazier.
16.Heat seal Strength
Strength of heat seal measured after the seal is cooled.
17.Laser Scoring
Use of high-energy narrow light beam to partially cut through a material in a straight line or shaped patterns. This process is used to provide an easy-opening feature to various types of flexible packaging materials.
18.LDPE
Low density, (0.92-0.934) polyethylene. Used mainly for heat-seal ability and bulk in packaging.
19.Laminated Film: A composite material made from two or more layers of different films, offering improved barrier properties and durability.
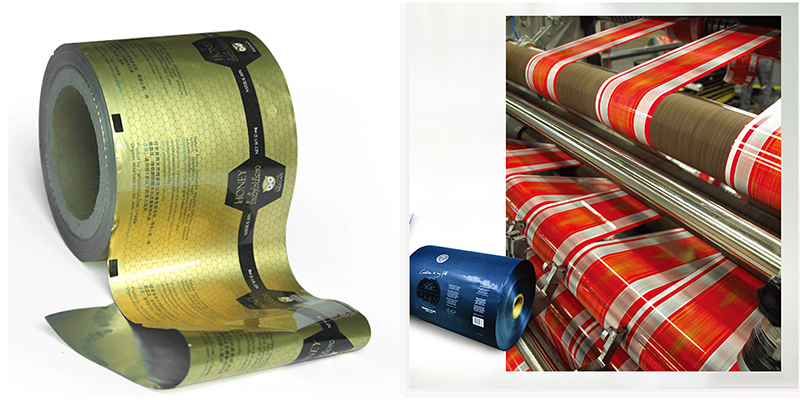
20.MDPE
Medium density, (0.934-0.95) polyethylene. Has higher stiffness, higher melting point and better water vapour barrier properties.
21.MET-OPP
Metallised OPP film. It has all the good properties of OPP film, plus much improved oxygen and water vapour barrier properties, (but not as good as MET-PET).
22.Multi-Layer Film: Film that is composed of several layers of different materials, each contributing specific properties such as strength, barrier, and sealability.
23.Mylar: A brand name for a type of polyester film known for its strength, durability, and barrier properties.
24.NY – Nylon
Polyamide resins, with very high melting points, excellent clarity and stiffness. Two types are used for films - nylon-6 and nylon-66. The latter has much higher melt temperature, thus better temperature resistance, but the former is easier to process, and it is cheaper. Both have good oxygen and aroma barrier properties, but they are poor barriers to water vapour.
25.OPP - Oriented PP (polypropylene) Film
A stiff, high clarity film, but not heat sealable. Usually combined with other films, (such as LDPE) for heat sealability. Can be coated with PVDC (polyvinylidene chloride), or metallised for much improved barrier properties.
26.OTR - Oxygen Transmission Rate
OTR of plastic materials varies considerably with humidity; therefore it needs to be specified. Standard conditions of testing are 0, 60 or 100% relative humidity. Units are cc./100 square inches/24 hours, (or cc/square meter/24 Hrs.) (cc = cubic centimetres)
27.PET - Polyester, (Polyethylene Terephthalate)
Tough, temperature resistant polymer. Bi-axially oriented PET film is used in laminates for packaging, where it provides strength, stiffness and temperature resistance. It is usually combined with other films for heat sealability and improved barrier properties.
28.PP – Polypropylene
Has much higher melting point, thus better temperature resistance than PE. Two types of PP films are used for packaging: cast, (see CAPP) and oriented (see OPP).
29.Pouch: A type of flexible packaging designed to hold products, typically with a sealed top and an opening for easy access.
30.PVDC - Polyvinylidene Chloride
A very good oxygen and water vapour barrier, but not extricable, therefore it is found primarily as a coating to improve barrier properties of other plastic films, (such as OPP and PET) for packaging. PVDC coated and ‘saran’ coated are the same
31.Quality Control: The processes and measures put in place to ensure that packaging meets specified standards for performance and safety.
32.Quad Seal Bag:A quad seal bag is a type of flexible packaging that features four seals—two vertical and two horizontal—that create corner seals on each side. This design helps the bag stand upright, making it particularly suitable for packaging products that benefit from presentation and stability, such as snacks, coffee, pet food, and more.
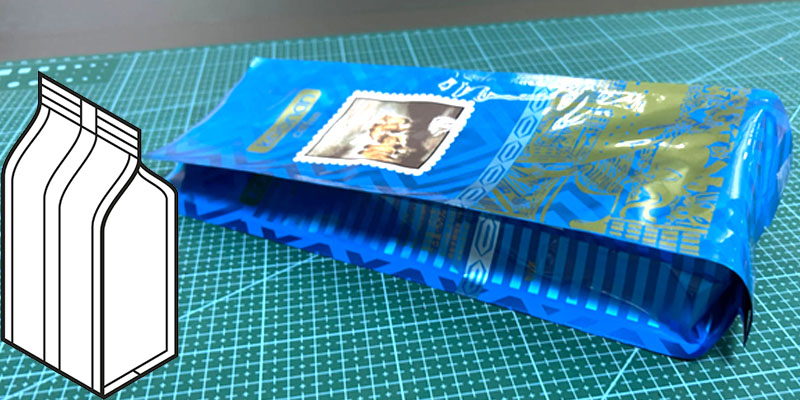
33.Retort
The thermal processing or cooking packaged food or other products in a pressurized vessel for purposes of sterilizing the contents to maintain freshness for extended storage times. Retort pouches are manufactured with materials suitable for the higher temperatures of the retort process, generally around 121° C.
34.Resin: A solid or highly viscous substance derived from plants or synthetic materials, which is used to create plastics.
35.Roll Stock
Said of any flexible packaging material that is in a roll form.
36.Rotogravure Printing - (Gravure)
With gravure printing an image is etched on the surface of a metal plate, the etched area is filled with ink, then the plate is rotated on a cylinder that transfers the image to the film or other material. Gravure is abbreviated from Rotogravure
37.Stick Pouch
A narrow flexible packaging pouch commonly used to package single-serve powder beverage mixes such as fruit drinks, instant coffee and tea and sugar and creamer products.
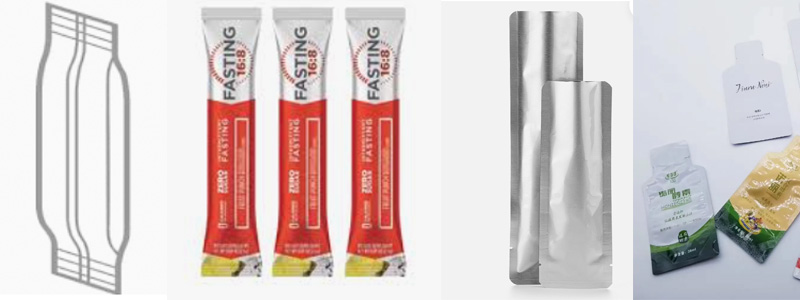
38.Sealant Layer: A layer within a multi-layer film that provides the ability to form seals during packaging processes.
39.Shrink Film: A plastic film that shrinks tightly over a product when heat is applied, often used as a secondary packaging option.
40.Tensile Strength: The resistance of a material to breaking under tension, an important property for the durability of flexible pouches.
41.VMPET - Vacuum Metallised PET Film
It has all the good properties of PET film, plus much improved oxygen and water vapour barrier properties.
42.Vacuum Packaging: A packaging method that removes air from the pouch to prolong freshness and shelf life.
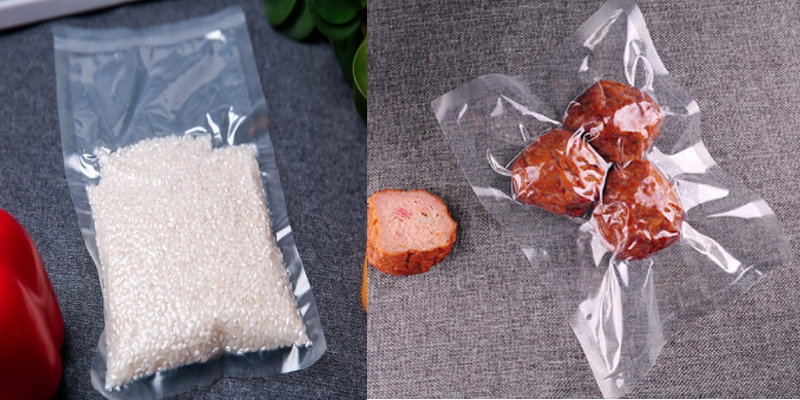
43.WVTR - Water Vapour Transmission Rate
usually measured at 100% relative humidity, expressed in grams/100 square inches/24 hours, (or grams/square meter/24 Hrs.) See MVTR.
44.Zipper Pouch
A recloseable or resealable pouch produced with a plastic track in which two plastic components interlock to provide a mechanism that allows for recloseablility in a flexible package.
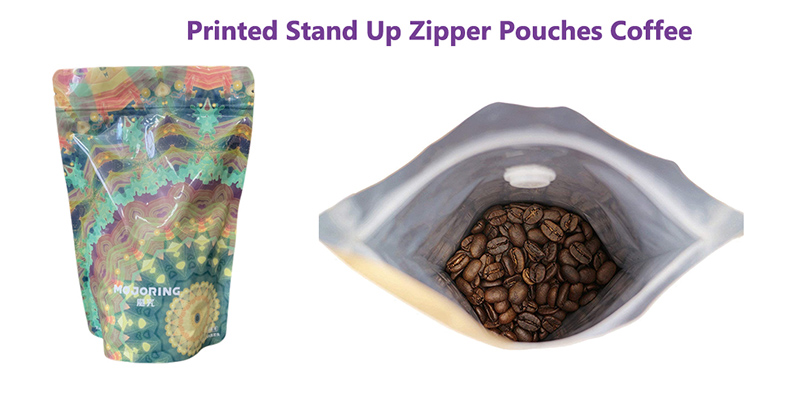

Post time: Jul-26-2024