Packmic has been audited and get the ISO certificate issue by Shanghai Ingeer Certification Assessment Co.,Ltd(Certification and accreditation Administration of PRC: CNCA-R-2003-117)
Location
Building 1-2, #600 Lianying Road, Chedun Town, Songjiang
District, Shanghai City, P. R. China
has been assessed and registered as meeting the requirements of
GB/T19001-2016/ISO9001:2015
Scope of approval Production of Food Packaging Bags within Qualification License .ISO certificate Number#117 22 QU 0250-12 R0M
First Certification: 26 Dec. 2022y Date: 25 Dec. 2025
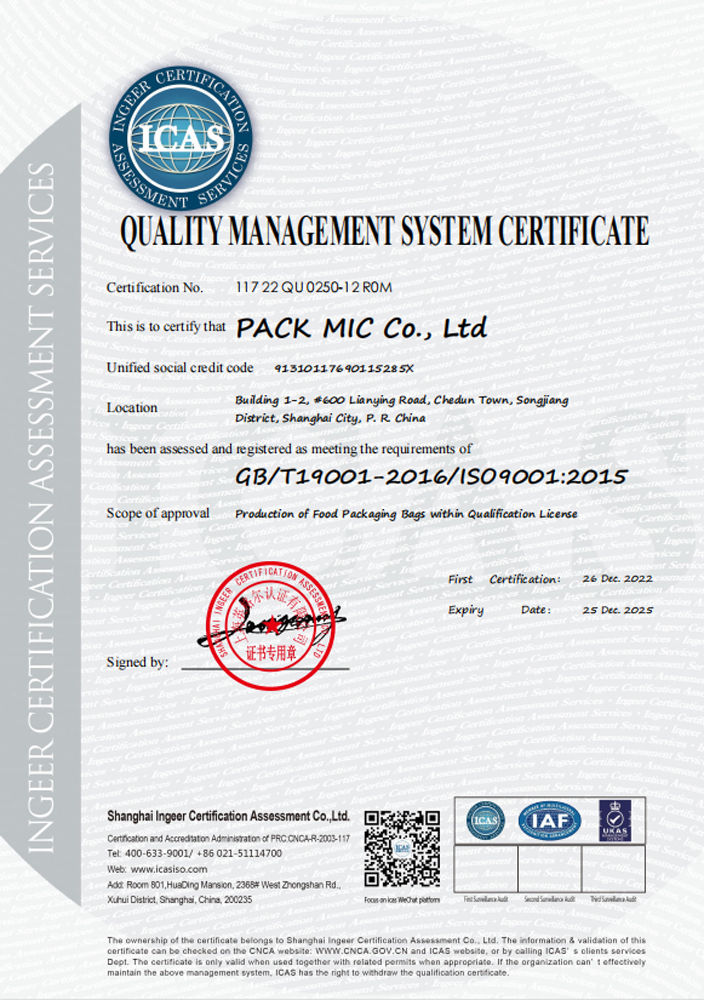
ISO 9001:2015 specifies requirements for a quality management system when an organization:
a) needs to demonstrate its ability to consistently provide products and services that meet customer and applicable statutory and regulatory requirements, and
b) aims to enhance customer satisfaction through the effective application of the system, including processes for improvement of the system and the assurance of conformity to customer and applicable statutory and regulatory requirements.
The standard is based on seven quality management principles, including having a strong customer focus, the involvement of top management, and a drive for continual improvement.
The seven quality management principles are:
1 – Customer focus
2 – Leadership
3 – Engagement of people
4 – Process approach
5 – Improvement
6 – Evidence-based decision making
7 – Relationship management
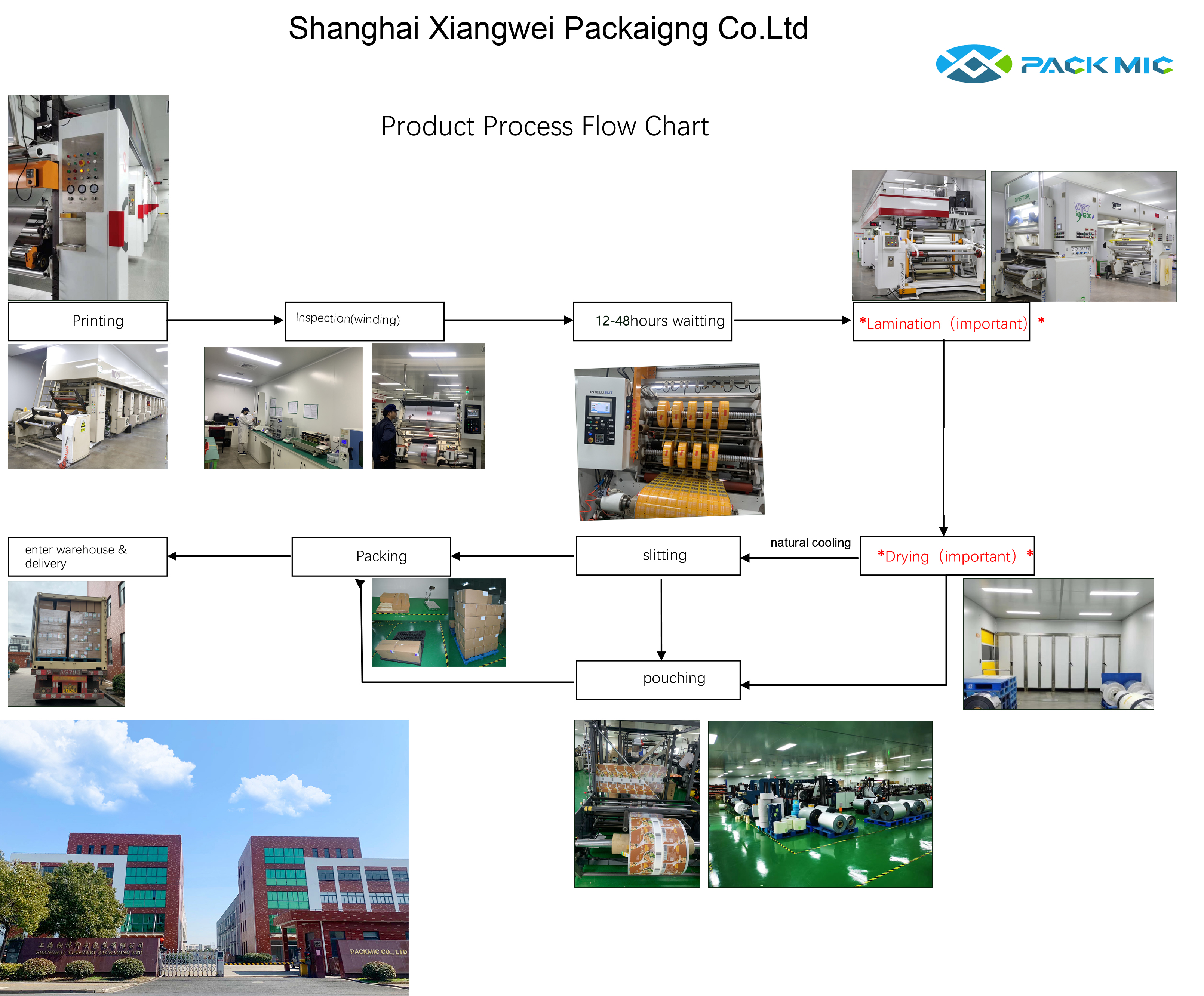
Key benefits of ISO 9001
• Increased revenue: leveraging the reputation of ISO 9001 can help you to win more tenders and contracts, whilst increasing efficiency aids customers satisfaction and retention.
• Improvement of your credibility: when organisations are looking for new suppliers, it is often required to have a QMS based on ISO 9001, particularly for those in the public sector.
• Improved customer satisfaction: by understanding your customers' needs and reducing errors, you increase customer confidence in your ability to deliver products and services.
• Higher operating efficiency: you can reduce costs by following industry best-practice and focusing on quality.
• Improved decision-making : you can detect and identify problems in good time, which means that you can quickly take steps to avoid the same mistakes in the future.
• Greater employee engagement: you can ensure everyone works toward one agenda by improving internal communications. Involving employees in designing process improvements makes them happier and more productive.
• Better process integration: by examining process interactions, you can find efficiency improvements more easily, reduce errors and make cost savings.
• A continual improvement culture: this is the third principle of ISO 9001. It means that you embed a systematic approach to identifying and exploiting opportunities to improve.
• Better supplier relationships: using best-practice processes contributes to more efficient supply chains, and certification will signpost these to your suppliers.
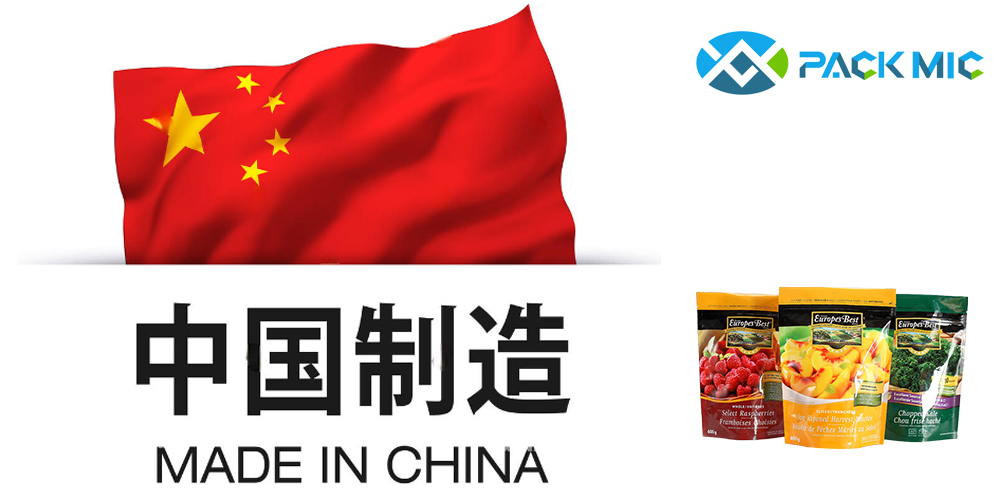
Post time: Dec-29-2022